CUSTOMER CASE PREEM
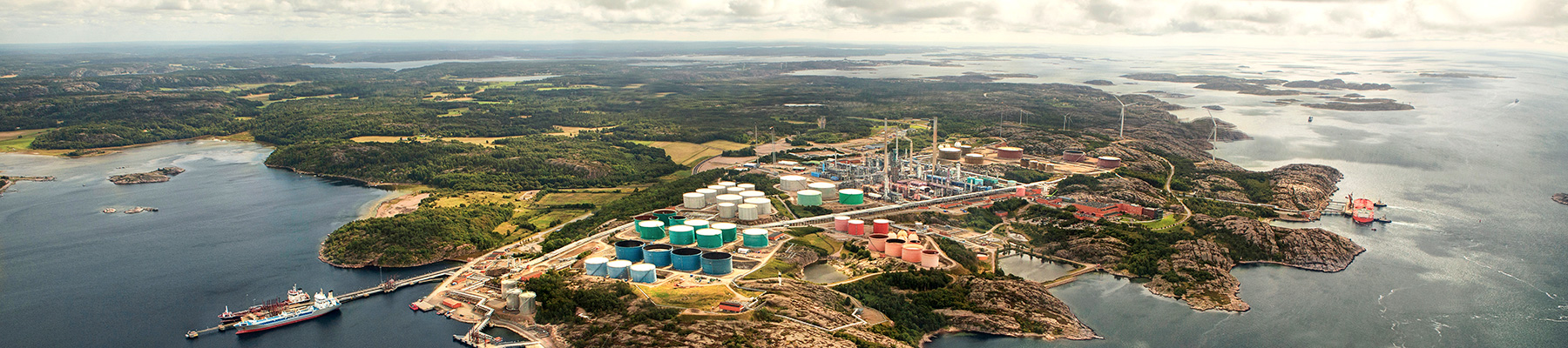
The Preem refinery in Lysekil is the largest facility of its type in Scandinavia and can refine up to 11.4 million tonnes of crude oil per year. The modern refinery is one of the most environmentally and energy efficient in Europe, and employs around 600 people.
Around one third of Preem’s production are distributed to the Swedish market, and the remaining two thirds are exported. Preem invests in renewable products and energy savings at its plants to reduce fossil carbon dioxide emissions. The company also plans to install effective control systems that will facilitate these environmental modifications.
The challenge
For several years Preem has been working with HSE consultants such as Swedish Standard Solutions Group AB (SSG) on tackling the hazard of electric arcs.
Attention had previously focused mainly on the hazard of electric shock, rather than the hazards of electric arc flash and incident energy. In addition, there is currently no specific Swedish standard that covers these hazards. Preem had relied on the US standards NFPA70E and IEEE1584 to calculate the incident energy. Based on this standard, the AG40 working group at SSG produced a guide – 'SSG 4510 Managing arc risks in electrical installations' – to help assess the risk and calculate incident energy, so that the right personal protective equipment (PPE) can be selected.
Preemraff has conducted risk assessments on around 85 switchgear sets in Lysekil and 40 in Gothenburg and used this information to calculate the incident energy of electric arcs. This work meant that the switchgear could be marked with incident energy information and an electrical safety matrix could be drawn up. This electrical safety matrix could then be used to help choose the appropriate protective equipment, among other things.
“We needed flame retardant workwear that gave protection from electric arc and was clearly marked with calorific values based on the calculated incident energy.”
- Klas Roos, Electrical Compliance Officer / Technical Engineer, Preem AB
Risk analysis for switchgear in the petrochemical industry
- Flame and heat
- Chemical splash
- Electric arc
Metal spatter
Radiant heat
Convective heat
Electric shock
Shock wave
Loud noise
Optical radiation
Toxic gas
Personnel who carry out electrical work on switchgear require flame retardant clothing that is certified to EN 61482-2 in combination with EN ISO 11612, since there is a risk of exposure to arc flashes. Clothing must often also meet the high visibility requirements of EN ISO 20471. In the petrochemical industry, Tranemo also recommends garments that are certified to EN 13034, EN 1149-5 and EN ISO 11612. Working with chemicals in an explosive / ATEX environment can influence the choice of protective clothing in many ways and choosing the right protective clothing can save a user’s life if an accident happens.
The solution
Preemraff in Lysekil provided valuable background information by calculating the incident energy of its switchgear. The aim was to identify all existing protection requirements and certifications for protective clothing. By presenting and providing tested protective clothing that suited the purpose, Tranemo helped Preem to identify a good protection solution that met its needs.
“After conducting a risk assessment, we recommended that Preem should use flame retardant Tranemo Skinsafe clothing – an effective multi-layer system – to guarantee a high level of protection from electric arc hazards. Because we have carried out all the necessary tests in accordance with EN 61482-1-1 for different combinations of garments, it was natural to offer Preem the right protection solution with clearly labelled standard compliance and the required incident energy levels.”
- Christer Almborg, Key Account Manager, Tranemo
The Preem refinery in Lysekil is a petrochemical plant where there is a risk of explosive atmosphere / ATEX and chemical hazards. Tranemo’s flame retardant solution for Preem also included protection against these risks in addition to electric arcs.
The result
Tranemo delivered a unique protection solution with high functionality that matched Preem’s risk situation and protection requirements.
“We have been using flame retardant clothing for a long time, but Tranemo’s flame retardant clothing was clearly marked with incident energies in cal/cm², which is exactly what we were looking for. Different combinations of garments had also been tested already, so we knew what protection we could get, with a good safety margin. Tranemo listened carefully to our requests and were great to work with.”
- Klas Roos, Electrical Compliance Officer / Technical Engineer, Preem AB